Jewelry Making Applications
- Flex Shafts for the Jewelry Maker
- Drill Bits & Burs for Making Jewelry
- Bur Applications in Jewelry Making
Flex Shafts for the Jewelry Maker
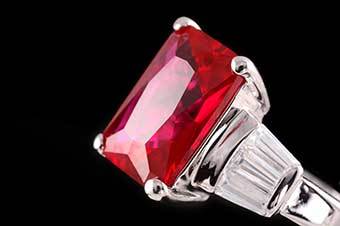
Flexible shaft machines make jewelry bench work much easier. They can be used for a variety of tasks, enhancing production and reducing fatigue. Since the flexible shaft was invented by Scottish engineer James Nasmyth in the 1800s, it has been used by jewelers and goldsmiths for drilling holes, setting stones, polishing metal, and shaping wax.
A flex shaft system uses a motor to rotate a flexible shaft. The end of the shaft contains a handpiece, which contains the desired-shape bit. It is operated by an adjustable power source. The flexible-shaft handpiece accessories may be burs, drill bits, polishing wheels, or brushes.
Pfingst & Company offers flexible shaft machines in various configurations. A wide variety of handpieces, sheaths and shafts may be selected. Often jewelers may have several different types of handpieces. Accessories, such as holders and bit organizers are available in our online flexible shaft machines catalog.
Drill Bits and Burs Used in Jewelry Making
Jewelers consistently use flexible shaft machines for repetitive bench work. Drill bits and burs are used in these machines to complete numerous tasks. Drill bits are used to make holes. Jewelry burs are most commonly used for engraving, filing, deburring, stone setting, and wax carving. There are dozens of burs to choose from. The jeweler must select the best drill bit or bur for the specific task at hand. Not only must it be the correct size and shape, but it should also be made from a material that will cleanly cut or finish the jewelry piece.
Burs are made from a variety of materials. Jewelry burs are made from tungsten vanadium steel, super carbide, high-speed steel, or diamonds. Steel burs and cutters are manufactured for working on precious metals and other softer materials. Carbide cutters are suitable for working on steel, precious metals, and their alloys. Diamond tools are suitable for working on hard materials such as glass, ceramic, porcelain, semi-precious stones, enamel, and precious metals. It is important to use a lubricant to keep the burs sharp and corrosion free. It will help them last longer, reduce friction, and produce a higher quality result.
Bur Applications in Jewelry Making
The following chart describes some of the various jewelry making bur applications.
BUR | BUR | BUR USE |
---|---|---|
Ball | round, pear, or oval shape |
expand a drilled hole
deburring drilled hole faux carving cutting curved surface versatile - range of dimensions |
Hart (Bearing) | cone shape with angles |
stone setting
create undercuts cut notches scoring and bending create textures |
Setting | cone shape | stone setting and cutting seats |
Bud | flower bud shape with gently curved taper |
stone setting
create tapered hole de-bur uses reposition a hole expand a drilled hole |
Flame | long, slim bud shape |
small stone seats
correct hole placement |
Cone | triangle cone shape |
clean up drilled hole
taper holes |
Inverted Cone |
wider upside down cone shape,
tapers toward the shank |
undercuts
cut tapered slots channel settings, inlays texturing |
Knife Edge | disk shape tapers to knife edge | cutting |
Krause | slim reamer shape |
enlarge holes
get into tight spaces |
Concave Cutter | cup shape, with inside teeth |
round spheres
round off prong or wire tips |
Wheel | disk shape, with cutting flutes on top and edge | remove metal from bezel |
Wax | various shapes | cut wax without clogging bur |
Cylinder | cylinder shape, straight sides |
remove specific metal amount
use as a rotary file |
Cross-cut | many shapes |
metal removal
remove large amount of material |
Finishing (Florentine) | cylinder, flame, bud, or barrel shape |
embellish surface
create satin finish |
Diamond | many shapes |
grinding burs
carve glass, stone, ceramic, metal |
Twist | corkscrew shape | drill holes |
Pearl drill | spade shape | drill holes in pearls |